Einleitung
Sie haben ein Lager? Aber kein Lagerverwaltungsystem (LVS)? Dann kennen Sie diese Bauchschmerzen:
- Wir müssen noch 20 Stück von den Automaten haben! Wo sind die?
- Wir finden die Lager nicht, Hr. Meier, der die eingelagert hat, ist heute Frei / ist in Rente
- Wo habt Ihr die Palette mit dem Überbestand für die Küchenrollen hingestellt?
- Wieso muss ich jedesmal den Gabelstapler holen, wenn ich den A-Artikel picken will?
- Wer hat diese C Artikel hier unten im Handbereich hingestellt?
- Wer hat die Lebensmittelverpackung direkt neben die Reinigungsmittel gestellt?
Usw. usw.
Ein typisches Lager, welches z.B. ganz ohne Lagerplatzzuordnungen oder auch mit festen Lagerplatz zu Artikel Zuordnungen arbeitet, sieht fast immer so aus:
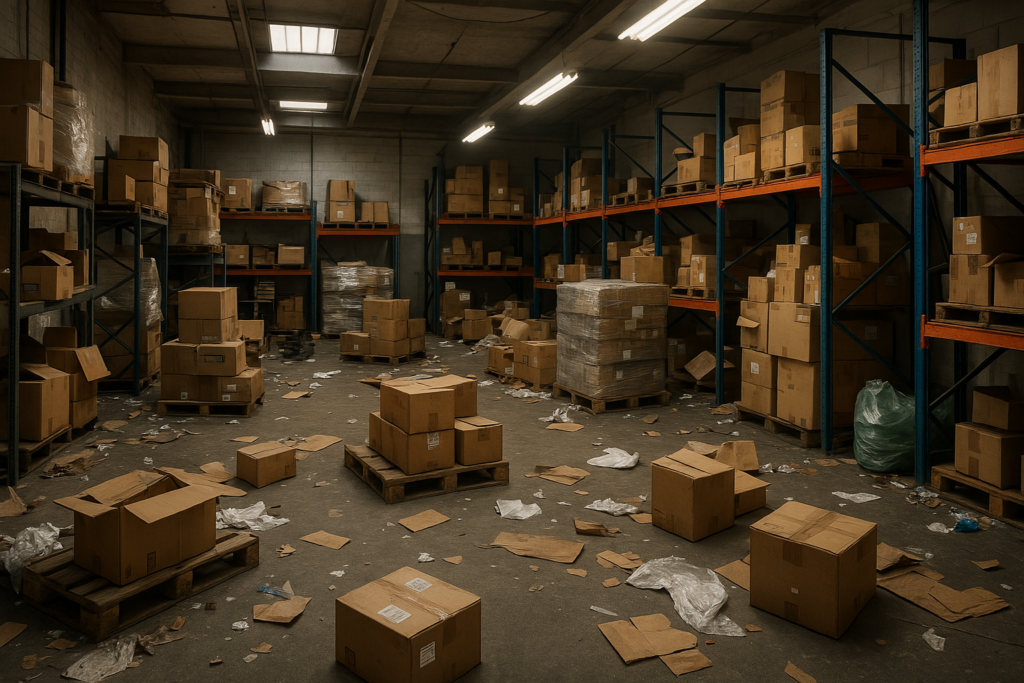
Was sehen wir in einem Lager ohne Lagerplatzzuordnung / mit fixer Lagerplatzzuordnung?
- Einzelne Lagerplätze sind völlig überfüllt
- Offensichtlich liegen Artikel in einer Art zusammen, welche eine lange Suchzeit erzeugen
- Läger dieser Art sind oft auch unordentliche Lager, da es immer zu wenig Platz für bestimmte Artikel gibt. Hierfür muss dann „irgendwo“ extra Platz in Anspruch genommen werden… diese Positionen sind aber nicht der EDV bekannt… und auch nicht allen Mitarbeitern.
- Aus Zeitnot, welche sich durch die unglaublich langen Suchzeiten ergeben, werden immer wieder Kartons umgelagert… oder besser umsortiert, unnötig aufgerissen, Restbestände nach dem Entnehmen nicht wieder ordentlich an ihren Platz zurück gelegt.
- Nicht direkt der Lagerhaltung geschuldet, sondern eher der damit einhergehenden Datenhaltung in der EDV: Hin und wieder werden „Pack-Artikel“ als einzelne Stück und „Stück-Artikel“ im ganzen Karton („Pack“) versendet. Während sich Kunden im ersten Fall noch melden, und zwar mit einer unangenehmen Beschwerde, wird es im zweiten Fall nur einen kostspieligen Fehlbestand geben, welcher aber im Nachhinein nicht mehr erklärt werden kann – Höhere Lagerhaltungskosten durch „Schwund“.
- Lagerplätze sind gänzlich ungleichmäßig gefüllt. Einige Lagerorte sind hoffnungslos überfüllt, während andere Lagerorte/Lagerplätze gähnende Leere aufweisen. Die Folge davon: Das Lager ist immer „zu klein“. Was es faktisch selten ist. Es wird nur zu viel Luft gelagert.
Im Gegensatz dazu ein „Chaotisches Lager“:
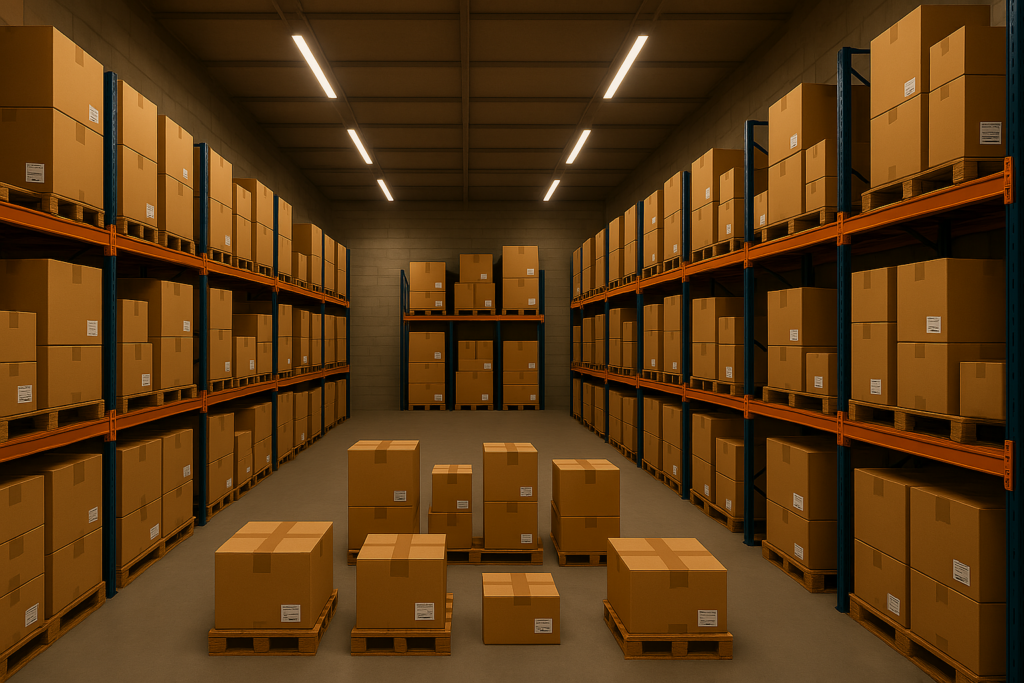
Was sehen wir in einem „Chaotischem Lager“ ?
- Man sieht den Plätzen von außen nicht an, welcher Artikel dort liegt
- Das Lager erscheint uniform, man kann sich nicht an Themen (wie „Spirituosen“ oder „Weihnachtsmänner“) orientieren
- Das Lager wird wesentlich kompakter ausgenutzt, es wird weniger „Luft“ eingelagert.
Um aber dies besser zu verstehen, müssen wir den Begriff „Chaotisches Lager“ oder „Chaotische Lagerordnung“ erst einmal definieren bzw. erklären. Den unter „Chaotisch“ stellt man sich erst einmal ein sehr unordentliches Lager vor, und nicht gerade das Gegenteil, ein erstklassisch organisiertes Lager ohne langes Suchen und mit keinem Abfall, und dazu noch mit wenig „Luft“ im Lager.
Chaotisch kommt hier aus der Urzeit der EDV. Denn ohne moderne EDV gibt es gar kein Chaotisches Lager… es kann bzw. konnte es nicht geben, der händische Verwaltungsaufwand hätte alle Dimensionen gesprengt.
„Früher“ war es das Maß aller Dinge, im Lager einem spezifischen Artikel einen genauen Lagerplatz zu geben. Das sehen Sie heute noch bei Aldi und Lidl im Kundenbereich (und nur dort!!): Spülmittel steht immer hinten rechts im letzten Gang zu den Kassen, und alle Spülmittel stehen neben- oder untereinander. Das gleiche bei Toilettenpapier, oder bei Fruchtsäften (dann aber im Eingangsbereich).
Das ist sehr Kundenfreundlich, und -genaugenommen- auch sehr Mitarbeiterfreundlich. Jeder Kunde und jeder Mitarbeiter weis nach wenigen „Entnahmen“ (= Picks), wo Er/Sie Käse oder Brot oder Schokolade findet. Und hat man erst mal die Schokolade gefunden, findet man auch schnell die Toblerone.
Ebenso einfach war die datentechnische Zuordnung: Pro Artikel wurde in der Datenbank ein Feld vorgehalten mit „Lagerort“. Und schon konnte man wunderbar einfach Inventurlisten oder auch Pickaufträge ausdrucken: Einfach nur den Auftrag oder die Inventurliste nach Lagerort sortiert ausgeben: Fertig!
Dies war bereits ein gewaltiger Fortschritt in der Lagerhaltung! Auf diese Weise konnten auch sehr ungeübte Aushilfen sich schnell im Lager orientieren, schnell einen bestimmten Lagerplatz (bei sinnvoller Sortierung) ansteuern und dort (hoffentlich….) den richtigen Artikel entnehmen.
Das sind doch alles Vorteile!
Wo liegen die Nachteile eines Lagers mit fixen Lagerorten/Lagerplätzen pro Artikel?
- Vordefinierte Lagerplätze sind *immer* zu klein oder zu groß.
–Zu groß: Wenn der Warenbestand eines Artikels abnimmt, so wird im gleichen Mase „Luft“ eingelagert. Irgendwann ist der Artikel nahezu aufgebraucht, das Lagerfach beinhaltet dann zu 90% Luft.
–Zu klein: Wenn dann wieder ein Halbjahresvorrat kommt, passen evtl. nicht alle Artikel in das zugeordnete Lagerfach. Noch schlimmer: Wenn -z.B. wegen drohendem Engpass wegen einer Pandemie oder günstigen Konditionen- eine deutlich größere als ursprünglich geplante Menge angeliefert wird, ist der zugeordnete Lagerplatz auf jeden Fall zu klein. - Wenn eine Warenanlieferung nicht in den vorhandenen Platz passt, wird „irgendwo“ ein Plätzchen für den Überbestand gesucht. Oft ist das in den -nicht so gut pickbaren- Plätzen über dem jeweiligen Artikel, aber auch dort ist dann manchmal kein Platz, und so wird der Kram dann irgendwo ganz anders abgestellt… evtl. auch irgendwo mitten im Weg oder in artikelfremden Umgebungen (im Kühlbereich, im Nicht-Kühlbereic, unter Lichteinfluss, usw. usw.)
- Es werden IMMER bei so einem Lager irgendwelche Artikel irgendwo abgelegt, wo sie nur ein sehr kompetenter Lagermitarbeiter wiederfindet… oder eben auch niemand wiederfindet, „weil der Erhardt gerade Urlaub hat“.
- So verkehren sich günstige Großeinkäufe durch „Schwund“ (weil die Artikel nicht mehr wiedergefunden werden) auch gerne einmal in ihr Gegenteil: Statt dem günstigen Einkauf hat man unwiederbringliche Artikelfehlbestände.
- Suchzeiten: Irgendwann sind die Artikel im originären Lagerplatz aufgebraucht, und es geht die Suche los, wo die Überbestände liegen. Oft, leider viel zu oft, wird dann, wenn man sie denn nach langer Suche (Zeit = Geld) gefunden hat, aus diesem Bestand gepickt, ohne jedoch diesen Bestand an den richtigen, in der EDV hinterlegten Lagerplatz zu verbringen („Umzulagern“). Somit wird nun auch jedes FiFo-Prinzip (First IN, First OUT, älteste Bestände werden zuerst ausgeliefert) zerstört. Gleitende Einstandspreise repräsentieren dann nicht mehr den echten Lagerwert, ältere Artikel verschmutzen oder verderben (Auch Gummididchtungen härten irgendwann einmal aus…), Verpackungen werden durch ständiges hin- und hergeschiebe beschädigt… Sie kennen das! Spätestens wenn man im REWE die frischere Milch VOR der älteren Milch im Kühlregal vorfindet, versteht man das hier beschriebene Dilemma.
- Inventuren brauchen durch die eben beschriebenen Suchzeite („Hier MUSS noch irgendwo eine LKW Batterie rumstehen! Die EDV sagt das!“) ein vielfaches der veranschlagten Zeit und bringen dazu noch immer arbeitsintensive Nacharbeit („Du! Ich habe eben doch noch die ausgebuchte LKW Batterie gefunden! Stand im Klo hinter den Ravioli-Dosen“).
- Bei nur knapp zu kleinem Lagerfach werden Verpackungen durch „Ich muss das jetzt hier alles reinquetschen“ beschädigt und können damit auch den Verkaufswert reduzieren oder einen Artikel schlimmstenfalls unverkäuflich machen -> zusätzlicher Verlusst.
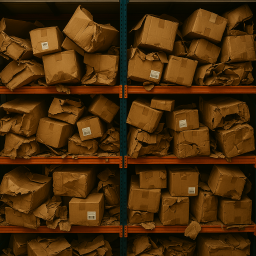
Was macht ein chaotisches Lager, ein chaotisches Lagerverwaltungssytem so viel besser?
In einem chaotisch organisiertem Lager wird jedem Wareneingang ein neuer, am besten optimal zu dessen aktueller Größe passender, Lagerplatz zugewiesen. Spülmittel Blau steht dann neben Kugellager und unter den Taschentüchern. Darum die Bezeichnung „Chaotisch“, weil es uns Menschen im Lager so erscheint. „Ordentlich“ wird es nur und erst durch Hilfe der EDV. Ein Wareneingang vom 1000 Zündkerzen (z.B. Palettenlager, Vorratslager) kann wo ganz anders abgestellt werden wie ein Wareneingang mit 25 Zündkerzen (A-Zone, Pickroboter, Handlager)
Einfache Einlagerung auch von unvorhergesehen großen Liefermengen
Große Wareneingange werden dynamisch auf Gebindegrößen (z.B. Kartons, oder Norm-Kisten) herunter gebrochen. Somit kann ein spezifischer Artikel wie Sicherungsautomaten dann an ganz unterschiedlichen Stellen im Lager liegen.
Automatische Lagerredundanz
Somit ergibt sich auch automatisch eine Redundanz: Wenn z.B. ein AKL (Automatisches Kleinteilelager, ein Regalbedingerät, ein Pickroboter) ausfällt, so lässt sich ein bestimmter Artikel mit hoher Wahrscheinlichkeit noch irgendwo anders im Lager finden.
Die Wahrscheinlichkeit von Fehlpicks durch ähnliche Artikel wird reduziert.
Bei Chaotischen Lagersystemen versucht man ganz gezielt, ähnliche Artikel, wie z.B. Schrauben M3x6, M3x8, M3x10, weit auseinander zu platzieren. Nicht jede studentische Aushilfskraft kann eine M3x6 von einer M3x8 unterscheiden… aber praktisch jeder Helfer (auch da gibt es Überraschungen…) kann eine M3x6 Schaube von einer 10er Mutter oder einer Leuchtstoffröhre unterscheiden.
Chargen, MHD, Seriennummernreine Bestände
Jeder Wareneingang wird als einzelner Lagerbestand mit einem eigenen Lagerfach/Lagerplatz behandelt. Hierdurch kann Navision/Business Central zu jedem einzelnen der eingelagerten Bestände mitteilen,
- Wann
- Von wem
- Wohin (Der Einlagervorgang ist erst beendet, wenn der Mitarbeiter das Ziel-Lagerfach gescannt hat)
dieser Bestand eingelagert wurde. Alle Meta-Daten des Wareneinganges (Lieferscheinnummer des Lieferanten, Bestellnummer von uns, Mindest-Haltbarkeitsdatum (so denn erfasst), Seriennummer, Chargennummer etc. bleiben bei diesem Bestand, bis er aufgelöst (komplett ausgelagert) wurde. Diese Daten „überleben“ auch eine Umlagerung. Standardmässig wird es vom System unterbunden, Bestände mit unterschiedlichen Meta-Daten zusammen zu mischen.
Optimierte Pickreihenfolge
Unter geziehlter Aufweichung der FIFO-Regeln kann eine Wegverkürzung beim Picken erzeugt werden, indem ein günstiger gelegener Bestand anstelle eines älteren Bestandes bevorzugt wird, oder z.B. ein Bestand mit einer exakt zur Pickmenge passenden Menge herangezogen wird, anstatt größer Gebinde aufzureisen oder mehrere kleinere Gebinde zusammen zu tragen. Hier greifen dann unternehmensspezifische Lagerregeln, da z.B. gerade bei Lebensmittel die beschriebene Optimierung bei einigen Artikeln gezielt NICHT erwünscht sein könnte.
Optimierte Lagerplatzausnutzung
Da durch das Auflösen von Wareneingängen in einzelne Bestände genormte Lagerplätze oder auch Normbehälter („Eurobehälter“) genutzt werden können, kann der Wareneingang mit aufwändiger Qualitätskontrolle und exakter Zählung (benötigt besser ausgebildetes Personal!) von dem folgenden echten physikalischem, sehr viel einfacherem Einlagern in das Lager getrennt werden. Außerdem können so Bestände in optimale Behälter/optimale Lagerfächer verbracht werden, was die Einlagerung von „Luft“ drastisch reduziert.
Nachträgliche Lageroptimierung & ABC-Analysen
Ergibt sich zur Lebenszeit eines Artikels ein kleinerer Raumbedarf (Bestände sind gesunken) oder ein seltenerer Zugriff (A-Artikel werden zu B oder C Artikeln), so können durch die Nutzung von z.B. Eurobehältern, Normkisten, Paletten einfache Umlagerungsaufträge durch den Computer erstellt werden, und vorhandene Bestände können ohne Verlust von Meta-Daten („MHD“, Chargennummern) von z.B. einem sehr gut zu erreichendem A-Pickplatz auf einen weniger leicht zu erreichendem C-Pickplatz umgelagert werden.
Automatischer Nachschub
Auch hier kann wieder die EDV helfen, indem automatisierte Nachschublisten generiert werden, um Überbestände aus Vorratslagern in die A-Zonen umzulagern.
Drastisch reduzierte oder gar komplett wegfallende Inventuren
Da Navision / Business Central bei jeder Kiste, jedem Fach, jedem Bestand die Sollmenge weiß, sind viele Picks gleichzeitig auch Null-Durchgangs-Inventuren.
Schickt beispielsweise Business Central/Navision einen Picker zu der Kiste 0815/4711, und weist ihn an, aus dieser Kiste die restlichen 23 Stück zu entnehmen, wird während des Picks automatisch geprüft, ob die 23 noch da waren (sonst hat der Mitarbeiter die Pickmenge beim Picken reduziert = Fehlbestand, und ob die Kiste nun leer ist (Rückfrage an den Picker, ob Kiste leer -> evtl. Mehrbestand). I.d.R. werten Wirtschaftsprüfer diesen Vorgang als Permanente Inventur, so dass eine echte Stichtagsinventur gar nicht mehr notwendig ist.
Warum ist dann nicht jedes größere Lager „Chaotisch“ organisiert?
Das stammt tatsächlich aus den Anfängen der EDV-gestützten Lagerführung! Wie weiter oben beschrieben, war die fixe Lagerplatzzuordnungen, welche schon auf Karteikarten möglich war und in den ersten Warenwirtschaftssystemen auch kinderleicht abzubilden war, ein enormer Komfortgewinn und eine enorme Arbeitserleichterung, verglichen mit dem „Nur der Chef weiß, wo was liegt“ der früheren Zeiten.
Und diese Lösung war so gut und so einfach zu verstehen, das sie sich einfach als „gut genug“ gehalten hat! Doch wie wir alle wissen, hat die IT, die Computerunterstützung seit dem enorme Fortschritte gemacht. Nur sind die Gedanken der Entscheider diesen Fortschritten eben noch nicht gefolgt.
Heutige IT-Lösungen, wie z.B: Navision Financials (ja, auch dafür habe ich ein LVS!) oder neu Business Central, haben mit der Datenmenge, wenn man sie denn Programmtechnisch korrekt verwaltet, kein Problem mehr!
Was unterscheidet meine LVS Lösung von der original in Business Central oder Navision enthaltenen Lagerverwaltung?
Eigentlich alles… vor allem die Bedienung, die (Um-)reservierung, die getrennte Bestandsführung… Sehen Sie sich bitte diese Aufgabenbeschreibungen hier an.
- Datenhaltung – die Bestände werden ganz anders verwaltet als im „Normalen“ Navision / Business Central
- Umlagerungen und Protokolle – auch diese werden gänzlich anders, viel schneller und kompakter- vorgehalten.
- Bestände – Mein LVS „Denkt“ von Anfang an in Beständen, nicht in Bewegungen, wie das Navision / BC365 eben – und aus gutem Grund! – tun.
Ich arbeite hier gerade noch an bebilderten Beispielen aller typischen Lager-Prozesse, bitte kontaktieren Sie mich oder schauen Sie gerne später noch einmal hier rein. Dieser Artikel wird derzeit ständig weiter entwickelt.